ALBA Synchrotron
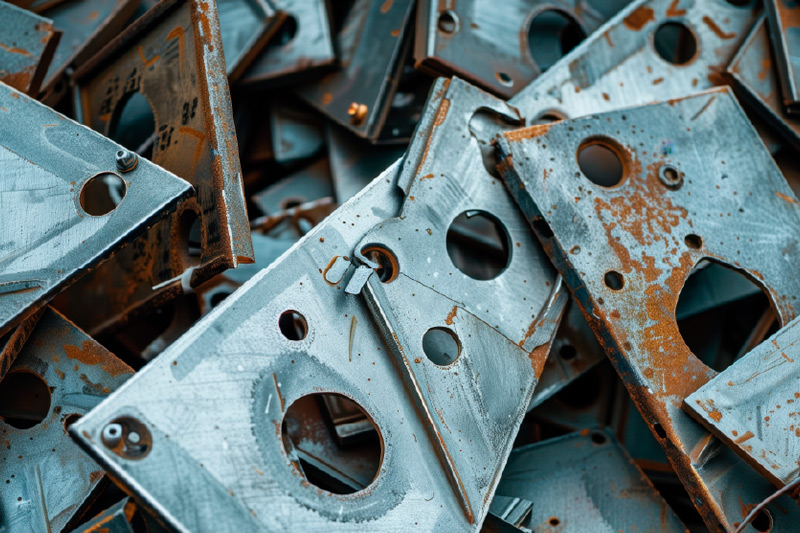
The European project CiSMA, coordinated by the technology centre Eurecat and with a budget of nearly €4.5 million, is to develop 100 percent recycled steel made from scrap and produced in an electric arc furnace to help cut CO2 footprint, boost circular economy and reduce EU’s dependency to critical raw materials in the automotive, professional laundry equipment and other industries.
The European steel industry is targeting a 50 percent reduction in CO2 emissions by 2030 and carbon neutrality by 2050. Electric arc furnace steel production, which replaces the traditional blast furnace process, “will make possible to produce high-performance steels for mass-market products,” says Jaume Pujante, PhD, CiSMA’s technical coordinator and head of the Metals Processing research line in the Metallic and Ceramic Materials Unit at Eurecat. “This will help to cut down emissions by more than 75 percent and use up to 100 percent scrap loads.”
To do this, the project will “tackle the challenge of producing high-performance steel with electric arc furnaces, a technology which is currently limited by the fact that low-performance scrap materials contain unwanted trace elements which adversely affect steel quality” adds Begoña Casas, PhD, CiSMA project coordinator at Eurecat.
CiSMA will maximize the use of low-quality scrap, separating undesired inclusions with a focus on copper. To validate the project’s developments, two pilot tests will be run to verify that the material and process are compliant to the market and also to demonstrate the technologies developed and quantify the environmental improvements compared to the current product.
One of the pilots will test components from a Volvo Cars vehicle and the other will evaluate components for Electrolux Professional washing machines.
The CiSMA project is additionally to “develop technologies that enable introducing these scrap-based, electric arc furnace steel products into mass-market sheet metal consumer goods”, notes Montse Vilaseca, PhD, director of Eurecat’s Metallic and Ceramic Materials Unit.
These technologies will furnish companies with access to fast metallic material characterisation tests for quality control, new methodologies to maximise the use of scrap in new steel manufacturing processes, a machine learning-based finite element modelling tool and digital twins.
In particular, at the ALBA Synchrotron fast and advanced microstructural characterization analyses will be performed to determine the phase morphology and composition of steel and to understand how scrap affects the base steel at the nanoscale. To do so, the project will develop and implement pipelines to combine analytical techniques and quickly obtain and analyze large amounts of data.
The project is funded by the European Union’s Horizon Europe programme and involves a consortium of twelve partners from five European countries: Spain, the Netherlands, Austria, Sweden and Belgium. Eurecat Technology Centre is the coordinator, and the other members are Tata Steel Nederland, voestalpine, Volvo Cars, Electrolux Professional, RISE Research Institutes of Sweden, Blekinge Institute of Technology, the ALBA Synchroton (ALBA-CELLS), Aerobase Innovations, the European Steel Technology Platform (ESTEP), the CSIC and the University of Liège.